Building a manufactured home: A closer look at how manufactured homes are built
Apr 17, 2024
•4-minute read
The surge in home prices and the continuing lull of housing starts means potential home buyers are searching for affordable alternatives. Building a manufactured home has emerged as a cost-effective solution to the old, conventional way to find a home.
Despite lingering misconceptions, manufactured homes offer a level of quality and durability that rivals traditional site-built homes.
This article will explain the benefits and processes involved in building a manufactured home, debunking myths and showcasing how it can be a viable option for both first-time home buyers and seasoned investors.
What is a manufactured home?
A manufactured home is a prefabricated structure. Skilled workers build the home in a factory and then transport it to a permanent location. This method of construction has evolved significantly since the birth of the “mobile home,” leading to improved quality and safety standards.
Unlike mobile home constructions, which predate the 1976 HUD code, the manufactured homes of today have to meet strict federal guidelines, ensuring durability, safety and energy-efficiency.
How are manufactured homes built?
The construction of a manufactured home or prefab home is a carefully planned and executed process, distinct in many ways from traditional home building. At its core, this process emphasizes efficiency, quality control and adherence to federal standards set by the HUD code.
Manufactured homes are often confused with modular homes but there are significant differences between the two. Modular homes, while also factory-built, are assembled on-site and must comply with local — not federal — building codes. That distinction offers a different set of advantages and constraints.
Construction timeline of a manufactured home
If you’re considering a manufactured home, it’s a good idea to understand what the building process is like first. Here’s an overview of what you can expect.
Step 1: Site preparation
Building a manufactured home begins with selecting and preparing the site. If the site has undeveloped land, this means clearing the site of trees, rocks, debris, and so on, ensuring the boundaries are marked clearly, and confirming that the site is level.
Access to utilities is also established during this phase, setting the foundation for a smooth installation process. This preparation is vital for the stability and longevity of the home.
Step 2: Securing permits and understanding zoning laws
Before construction can begin, it's essential to navigate the legal landscape by securing the necessary building permits and understanding the local zoning laws.
This process, which can take 6 – 9 weeks, ensures that the construction complies with all local regulations and standards, paving the way for a legally sound and compliant home.
Step 3: Designing your manufactured home
With legalities in place, you can move on to designing your manufactured home. This stage offers a range of preset designs and customization options, allowing buyers to choose floor plans and upgrades that reflect their style and meet their needs.
From hardwood floors to upgraded cabinetry, this process personalizes the home for comfort and functionality.
Step 4: Off-site construction begins
Manufactured home construction starts in a controlled factory or warehouse environment, where the foundation, floors, walls and roof are assembled with professional precision. The electrical wires, plumbing lines and installation are added during this stage as well.
This phase benefits from the efficiency and quality control possible in a factory setting, with materials and components constructed and assembled with precision.
Step 5: Adding final touches in the factory
As the structure takes shape, final touches — such as the installation of drywall, windows and siding — are completed. The home is then painted, and any finishing touches are added, resulting in a ready-to-install manufactured home.
Step 6: Inspection and certification
Before leaving the factory, the home undergoes rigorous third-party inspections to ensure it meets all HUD standards for manufactured housing. Successful inspections result in the home receiving a certification seal; meaning it has met its compliance and is ready for installation.
Step 7: Delivery and installation
The final step involves transporting the manufactured home to its prepared site and installing it securely. This process includes attaching the home to ground anchors and reinforcing it with steel straps, ensuring its stability against environmental forces such as storms and strong winds.
The overall manufacturing process—from site preparation to installation—shows the efficiency, safety, and quality involved in building a manufactured home.
How much does it cost to build a manufactured home?
One of manufactured homes' most appealing attributes is their affordability, with the U.S. Census Bureau reporting an average cost of $128,000.
However, several factors influence this price, including:
- The state you live in
- The cost of land
- The size of the home and the customizations you choose to make
Community living versus buying land
When comparing the cost of community living versus buying land, it's important to consider the long-term implications. Living in a manufactured home community often involves the cost of lot rental but comes with amenities like swimming pools, tennis courts and walking trails that you wouldn't have if you purchased land independently.
Both options have their advantages, depending on your lifestyle and financial goals.
Should you buy or build a manufactured home?
Manufactured homes also offer benefits beyond affordability. They are constructed with quality and durability in mind, in addition to the strict federal standards that ensure safety and energy efficiency.
Their longevity is often comparable to that of traditional site-built homes, with the added versatility of relocation. The manufactured home construction process also allows for quicker occupancy compared to traditional homes, making it an efficient solution for many homebuyers.
Quality assurance and financing options
There were initial concerns regarding the quality of manufactured homes in their early years. However, studies done on manufactured homes from the 1990s onwards demonstrate that these homes can match the quality of site-built homes when properly looked after.
One such study, by the Harvard Joint Center for Housing Studies, concluded that manufactured homes placed on land owned by the homeowner have been shown to appreciate in value at rates comparable to site-built homes. The findings of this analysis emphasize that a variety of manufactured homes remain a cost-effective option, as much as 73% less expensive than similar site-built homes.
The bottom line: Manufactured homes are for family living
More and more, manufactured homes are being recognized as a practical, affordable housing solution to today's market challenges. They offer the quality, durability and comfort of traditional homes but at a fraction of the cost and with greater flexibility.
Are you interested in buying or building a manufactured home? Start the approval process with Rocket Mortgage® today to make your dream of homeownership a reality.
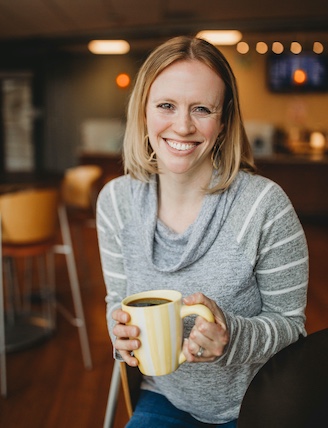
Jamie Johnson
Jamie Johnson is a Kansas City-based freelance writer who writes about a variety of personal finance topics, including loans, building credit, and paying down debt. She currently writes for clients like the U.S. Chamber of Commerce, Business Insider, and Bankrate.
Related resources
10-minute read
How to buy a mobile or manufactured home
Manufactured homes can be an affordable option for home buyers as traditional home prices rise. Learn about getting a mobile home loan from Rocket Mortgage.
Read more
6-minute read
Everything you should know about financing a modular home
A modular home is a type of prefabricated, manufactured home. Here’s what you should know if you’re considering financing a modular home.
Read more
3-minute read
What is a chattel mortgage and how does it work?
A chattel mortgage is an option for purchasing a manufactured home where the home secures the loan. See how chattel loans differ from traditional mortgages.
Read more